Alliance Industrial Solutions is pleased to continue our presenting sponsorship of the Evolution of Manufacturing Awards this year, celebrating local industry leaders for their innovation, creativity and positive organizational impact.
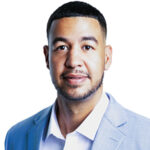
Chief Revenue Officer
Alliance Industrial Solutions
As we look ahead to 2025, manufacturing is set to embrace exciting innovations like advanced automation, sustainable production practices and smarter supply chain solutions. These technologies promise to revolutionize how manufacturers operate and compete, both locally and globally.
But even the most cutting-edge innovations rely on one essential factor: people. From assembly lines to boardrooms, the success of these advancements depends on the creativity, dedication and collaboration of employees. After all, technology may enable progress, but relationships are what drive it forward.
The connection between relationships and innovation is undeniable. Employees who feel valued and supported are more likely to take ownership of their work, collaborate effectively, and propose new ideas. When organizations foster an environment rooted in trust, open communication and empowerment, innovation thrives.
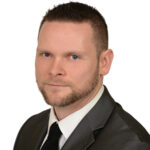
Chief Operating Officer
Alliance Industrial Solutions
Building workplaces where ideas flourish begins with prioritizing relationships. Open-door policies and regular feedback loops ensure employees feel heard. Comprehensive training programs and career development opportunities communicate that their growth matters. When your company prioritizes well-being, it sends a powerful message: you are more than a worker; you are a partner in our success.
This year’s honorees exemplify what’s possible when manufacturers invest in their people. By fostering strong relationships and empowering employees, these companies have driven meaningful innovation, embraced emerging trends and strengthened Northeast Ohio’s manufacturing community.
Congratulations to the 2025 Evolution of Manufacturing winners — your visionary leadership continues to inspire us all! ●
ADVERTISEMENT
2025 Evolution Honorees
AKS Cutting Systems is a machine tool manufacturer based in Cleveland, Ohio. The fourth-generation company delivers made-in-the-USA plasma and waterjet cutting systems for the heavy-fabrication industry. AKS Cutting Systems has been in operation for over 100 years and has developed a strong reputation for durability, accuracy and reliability.
AKS Cutting Systems has 65 employees and services businesses across the globe.
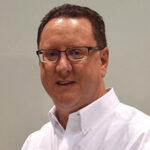
Greg Phillip
President
Over the past decade, AKS Cutting Systems has adjusted from contract manufacturing to supporting a full line of plasma and waterjet cutting systems. The company covers fully integrated CNC machinery that’s easy to use and completely customizable. The AKS team strives to deliver industry-leading machinery that helps reduce manufacturing costs and increase efficiencies. In 2012, AKS developed a first-of-its-kind five-axis beveling system called the “robo-kut.”
Its ½:1 capability exceeds traditional 1:1 ratios, making the robo-kut the most powerful five-axis plasma cutting bevel head on the market. This technology has been able to revolutionize many heavy fabrication industries. Boiler making, pier fabrication, turbine blade design, bridge fabrication, skyscraper creation and submarine fabrication are just a few. In 2024, the team combined the robo-kut with the new Hypertherm XPR plasma power supply. This makes it the most versatile unitized plasma system on the market. It’s able to process steel plates and tubing, complete weld prep, drill holes and carry out geometry marking all in one system. ●
Alco-Chem Inc. has been a family-owned business since 1969, employing several family generations throughout the years and a team of dedicated and knowledgeable employees. Its foundation was built on quality janitorial cleaning products, dietary products and laundry products, along with excellent customer service.
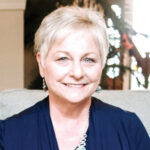
Owner and CEO
The company’s reach covers Northeast Ohio, and whereas many manufacturing companies have gone to more technological advances, its focus has been on going back-to-basics — being a solid, dependable and trustworthy company. Focusing on employees has been crucial to its culture and has funneled through all departments, including manufacturing, sales, service and machine repair. Its production manager has focused on training procedures and timelines within the manufacturing process and shoring up its line with dependable products. Inventory control with SKU rationalization has also been an important factor.
It has been critical to forecast for consumer and market trends to be as prepared as possible, with close attention paid to vendor relationships, pricing for raw materials and supplies, and having multiple suppliers to deal with shortages and abnormal spikes in pricing. Greater control over purchasing at the right time for the right price has also been an important factor. Focusing on the inside components has made a smoother process for sales and service in the field. ●
Since 1929, Biery Cheese Co. has been a customer-oriented provider of cheese products. The fourth generation family-owned company got its start with Norman and Laura Biery selling Swiss at farmers’ markets. Today, it operates large-scale cheese manufacturing facilities that provide custom and private label packaging and services.
Its extensive product line includes natural cheeses, specialty and artisan cheeses, kosher selections, plant-based cheeses and more that meet the highest standards in food safety and quality. Biery’s superior customer service and expertise with custom solutions provides products with the flavor profiles and packaging to fit a business’s unique needs.
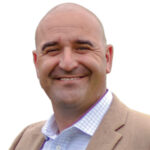
CEO
High-quality products are matched by high-quality facilities, following rigorous food safety standards, undergoing regular inspections and keeping up with industry certifications to help guarantee superior products that are as consistent as they are delicious. Facilities are SQF Level 3 certified, the highest attainable food safety assurance level within the global SQF code.
Biery works with customers to create innovative and competitive packaging options that are designed to accommodate concerns for product safety and ensure convenience. The company believes the right packaging is crucial to the efficiency and profitability it provides.
As it continues to grow, with more than 600 employees, it will always remember where it all began: with a dedication to quality that has won awards and earned trust. ●
Cantex Inc. began over 70 years ago as a division of Texas-Vitrified, a corporation serving the utility and building construction industry. As the plastics division grew steadily, product lines expanded into several major categories of PVC products. In the 1990s, these product lines were narrowed to the PVC electrical and communications products needed to supply a new, highly technical era, and the new Cantex emerged.
Cantex became dedicated to exceptional service as it provided electrical distributors, contractors and end users with a broad line of superior PVC electrical conduit and fittings, elbows, and non-metallic residential switch, outlet and ceiling boxes, to keep people powered and connected.
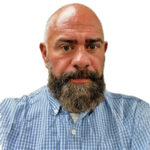
Production Manager
Cantex is now a leading producer of American-made PVC electrical conduit and fittings with manufacturing and distribution facilities strategically placed nationwide.
Its facilities feature some of the most modern production equipment and process technology in the industry, producing all-encompassing lines of PVC products to serve the power, utility, building construction and communications markets around the globe.
Cantex has invested in state-of-the-art equipment and well-trained people who focus on quality, innovation and money-saving logistics to deliver better product solutions and savings to customers.
Its quality PVC electrical products are available worldwide. In an ever-changing global market, Cantex continues to adapt to reach higher standards of customer support, quality and reduced impact on the environment. ●
As a family-owned and -operated manufacturing firm in Cleveland, Ferragon has created an operation that focuses on evolving the process of manufacturing with nearly flawless safety and risk controls.
From humble beginnings, Ferragon Corp has grown into one of the leading metals services providers in North America. Throughout its history, it evolved to meet the needs of the growing market with respect to steel, and has transitioned through several acquisitions of other firms. Its ongoing investment in the latest processing technologies and a commitment to service has enabled the company to provide ever increasing value to its customers.
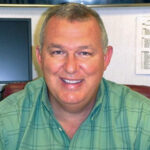
CEO
Ferragon continues to be a best-in-class provider, creating hundreds of jobs not only in Northeast Ohio but also in Michigan and in Texas. Within the global economy, it has become a large player in the steel industry, supplying the likes of Cleveland Steel and beyond.
By making strategic acquisitions, and with continued investment in innovation, Ferragon has stayed on the cutting edge of the steel industry, recruiting more employees and driving larger and larger sales. Not only is its investment in technology and automation creating streamlined efforts, but it has also not eliminated jobs. Instead, it’ created a larger mix of technology and a strong, committed workforce.
Looking to the future, Ferragon will continue to be a center for innovation in the steel industry here in Northeast Ohio and beyond. ●
Hynes Industries is a custom fabrication and roll form metal solutions manufacturer that has undergone a significant transformation over the past decade, investing in new capabilities and technologies to meet evolving market demands.
A notable milestone is the addition of an advanced in-line weld mill, which represents the largest single investment in the company’s history. This technology enables Hynes to produce closed-section profiles with superior strength, eliminating the need for costly secondary operations and delivering substantial time and cost savings to customers.
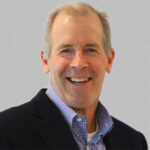
President and CEO
The company has also strategically focused on high-growth markets such as solar energy, automated material handling and truck/trailer manufacturing. These efforts have driven double-digit growth, supported by targeted investments in robotic welding cells and roll-forming lines, which increase capacity and enhance product quality.
Operationally, Hynes has integrated advanced ERP systems and data-driven processes, including ISO 9001:2015 certification, to ensure precision and reliability. This focus on quality is reflected in a 99 percent on-time fulfillment rate and consistently high customer satisfaction scores. Further, Hynes has embraced workforce development through enhanced training programs to upskill and retain top talent.
One significant challenge was meeting the increasing demand from high-growth markets like solar and automated material handling. Hynes responded by expanding its capabilities with new technologies, such as robotic welding cells and an in-line weld mill. These investments enabled Hynes to scale production without compromising quality. ●
North Coast Container has taken a proactive approach to staying competitive and meeting the needs of customers in an increasingly globalized marketplace. It has strategically expanded its operations through acquisitions, building a nationwide network that ensures operational redundancy and proximity to key markets. In 2023, it rebranded to unify its identity under the North Coast Container name, creating a stronger presence for global customers who value clarity and consistency from their partners.
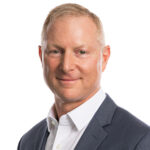
CEO
Facility modernization has been a major focus, with investments in advanced technology and automation that have enhanced efficiency and product quality, helping the company remain adaptable to the demands of an evolving global economy. Further, sustainability efforts aim to minimize waste and emissions while producing steel drums — the most recyclable packaging option available.
These initiatives have had a significant positive impact on every aspect of the business. Operationally, the adoption of advanced technology and the Toyota Production System have streamlined workflows, reduced waste and enhanced the company’s ability to meet customer demands with precision and reliability.
North Coast Container has built a reputation for dependability, quality and innovation, which it continuously reinforces through ongoing investments in people, processes and sustainability. As the largest independent steel drum manufacturer in North America, it meets the needs of global supply chains yet maintains the flexibility and personal service of a family-owned business. ●
OGS Industries is a leader in precision manufacturing, providing solutions to industries where accuracy, compliance and durability are nonnegotiable. With capabilities including metal stamping, fabrication, CNC and Swiss machining, and a focus on delivering high-quality parts and components, it supports critical industries such as aerospace and defense, medical, recreation and power sports, and transportation.
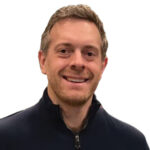
CEO
The organization has continually evolved to meet the challenges of a dynamic manufacturing landscape and global economy. Its growth strategy has been rooted in investing in both people and technology. In this past year alone, it has strengthened its leadership team with a vice president of sales to accelerate growth in the aerospace sector, and has invested millions in advancing its equipment and core capabilities.
New technology advancements and modernizations have also played a critical role in its growth and ability to meet customer needs. This year, it has invested millions of dollars in state-of-the-art equipment to enhance efficiency, quality and capacity.
OGS Industries is also an active member of the local community. By fostering meaningful partnerships and investing in early career development, it is shaping the future of manufacturing while empowering the young individuals who will drive it forward. It hopes its ongoing efforts, along with its commitment to advancing career opportunities, inspires people as it continues to build a legacy of innovation and growth for generations to come. ●
Evolution is the word that most appropriately describes the essence of Philpott’s sustained success for 135 years. This management philosophy has ensured Philpott’s continued leadership in the custom molded rubber and plastics products market sector.
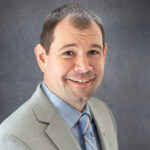
President and CEO
Having posted record sales, earnings and enterprise value in its most recent year, the results highlight the continued maturation of Philpott management’s most recent 10-year evolution plan to return its product manufacturing from China to the U.S. This plan also included market, product and customer expansion, and a strategic acquisition component. Philpott completed a full circle from two decades earlier, when manufacturing activities were outsourced to China, U.S.-based manufacturing was closed and remaining equipment was moved to other entities where contract manufacturing was undertaken. These actions, which were initiated in the mid 1990s, were necessary at a time when many of Philpott’s largest customers had moved operations to Asia. In hindsight, this offshoring strategy turned out to expensive as costs for increased transportation, quality problems and diversion of Philpott management attention kept the company from growing. This spurred the company move its manufacturing back to the USA.
Management is now optimizing its U.S.-based manufacturing processes and investing in new and upgraded machinery.
As a result of this evolutionary process, Philpott recorded its largest ever revenue in 2023 and has dramatically increased its domestic labor force. ●
Royal Chemical has strategically expanded its manufacturing operations to meet the evolving demands of a global economy. The company operates five facilities across the U.S. These strategically positioned facilities enable Royal Chemical to reach approximately 83 percent of the U.S. population within one business day, significantly reducing lead times and transportation costs.
Royal Chemical specializes in contract manufacturing, focusing on blending and packaging services that adhere strictly to customers’ proprietary formulations. This approach ensures that clients’ intellectual property is protected while benefiting from Royal Chemical’s advanced manufacturing capabilities. It employs state-of-the-art liquid and powder blending equipment to deliver customized solutions and is committed to sustainability, implementing eco-friendly practices such as waste reduction, energy optimization and the use of sustainable raw materials.
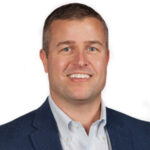
President and CEO
Operational enhancements have streamlined production workflows, increasing capacity and improving delivery times. The strategic distribution of facilities allows Royal Chemical to serve key markets more effectively, resulting in higher customer satisfaction and improved supply chain efficiency.
Royal Chemical brings significant value to its customers through specialized equipment and expertise. Utilizing advanced liquid and powder blending equipment, it ensures precise adherence to customer formulations, maintaining product integrity and quality. Comprehensive services offer end-to-end solutions — including blending, packaging, warehousing and fulfillment — allowing customers to streamline operations and focus on core business activities. And by leveraging economies of scale and strategic supplier relationships, Royal Chemical reduces production costs, providing customers with competitive pricing. ●
Skylift has built its reputation on manufacturing innovative easement and backyard machines, digger derricks and material handlers. With over 20 years of manufacturing expertise and thousands of units in operation, Skylift continues to deliver trusted and reliable solutions for challenging job sites.
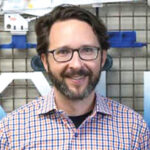
COO
Now, Skylift is introducing a new product line: Sky Trucks. This marks the company’s expansion into truck-mounted booms, a move that has diversified its production capabilities, leveraging the same engineering precision and operational expertise that have defined its easement equipment. It represents a new chapter in Skylift’s operations, enhancing its ability to meet broader customer demands.
The addition of truck-mounted products has increased demand for skilled manufacturing roles at Skylift’s Lorain, Ohio, facility, supporting local economic growth and reinforcing Skylift’s commitment to community-driven success. It also positions Skylift to capture new markets and customers while building on its reputation as a trusted industry partner. The SKY47 will serve as a foundation for further innovation in the Sky Trucks line, ensuring strong growth opportunities in 2025 and beyond.
Skylift’s success is rooted in its identity as a family-owned business, now spanning two generations. In addition to strong family leadership, Skylift’s success has been shaped by its tenured staff, many of whom have been with the company for over 20 years. This dedicated team has played a pivotal role in driving innovation, maintaining quality standards, and supporting Skylift’s growth into new markets. ●
Stakes Manufacturing is the leader in the production of high-quality, on-demand printed apparel, providing innovative solutions for a diverse range of clients.
It has continually invested in next-generation digital print capabilities, ensuring that clients receive the best quality and sustainable print solutions. Its advanced digital printing technology allows for greater customization, speed and precision, empowering clients to bring their visions to life with exceptional results. At Stakes Manufacturing, every client is unique, which is why the company offers customized services tailored to their specific needs. Whether it’s branding materials, packaging, or product labeling, the team works closely with each client to develop personalized solutions that meet their standards.
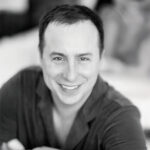
Co-founder
Beyond its technical expertise, Stakes Manufacturing is deeply committed to fostering an inclusive and supportive workplace. It recognizes the value of diversity and inclusion, which is why it has dedicated resources and initiatives aimed at providing meaningful employment opportunities for people with disabilities. Its workplace practices reflect an unwavering belief in the power of diverse perspectives and the importance of creating an environment where all employees can thrive.
As it grows, Stakes Manufacturing will continue pushing the boundaries of innovation, delivering exceptional service to its clients and setting new standards for inclusivity in the workplace. ●