Alliance Industrial Solutions is pleased to continue our presenting sponsorship of the Evolution of Manufacturing awards this year, celebrating local industry leaders for their innovation, creativity and positive organizational impact.
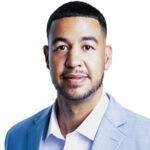
Chief Revenue Officer
Alliance Industrial Solutions
In 2023, Merriam-Webster’s Word of the Year was “Authenticity.” Along with the prevalent “Skills Gap,” these terms highlight key challenges and opportunities in manufacturing. Northeast Ohio is witnessing a convergence of traditional manufacturing authenticity with the advanced skills required for the industry’s future. This synergy is revitalizing the sector and bridging the skills gap, blending heritage with innovation.
Authenticity in manufacturing goes beyond preserving old techniques; it’s about integrating these with modern technology and innovation. This approach emphasizes ethical practices, sustainability and transparency. And it’s attracting a new workforce that seeks more than ‘just a job.’ This workforce desires skill mastery, growth, creativity, and flexibility — while still maintaining connection to manufacturing’s deeply rooted legacy.
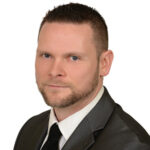
Chief Operating Officer
Alliance Industrial Solutions
To address the skills gap, companies are actively engaging in upskilling and reskilling their current employees through comprehensive training programs and collaborations with educational institutions. These initiatives blend traditional manufacturing skills with modern technologies like automation and AI, simultaneously appealing to the aspirations of young talent and providing a renewed sense of pride in the industry. This focus on internal development ensures that existing employees evolve alongside the industry, maintaining the authenticity and heritage of manufacturing while staying at the forefront of technological advancement.
This year’s honorees exemplify this movement, where authenticity and skill development coexist, opening limitless possibilities. Their efforts in blending respect for traditional manufacturing with modern innovation truly set a benchmark for the industry.
Congratulations to this year’s winners for their significant contributions to manufacturing in Northeast Ohio. We look forward to witnessing your continued evolution in the years to come! ●
ADVERTISEMENT
2024 Evolution Honorees
Led by President and CEO Michael Canty, Alloy Precision Technologies Inc. specializes in custom and standard manufacturing of bellows and flexible sealing assemblies, precision machining, welding, tubing and other highly engineered products.
In recent years, Alloy has continued to evolve and position itself to compete effectively in the global economy. The company
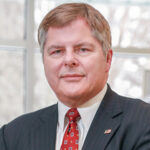
President and CEO
proactively invests in modern equipment, novel technologies and advanced processes to achieve a solid competitive advantage for its custom-engineered products.
Modern, advanced equipment is generally faster, more accurate and more productive, and built-in sensors gather performance metrics to drive decisions in real-time. This approach to manufacturing allows Alloy to produce quality parts in the U.S. that are competitive in the global marketplace. Examples include:
- CNC machining. More than 70 percent of Alloy’s 36 CNC machines are less than eight years old, offering advanced capabilities that hold tight tolerances. The company’s CNC equipment has been wired (IIoT technology) as part of its digital transformation to promote an understanding of equipment and personnel performance, driving equipment utilization and competitive value.
- Custom hydroforming. Alloy’s hydroforming equipment and required tooling are custom-designed and built to produce competitive, proprietary, superior bellows sold worldwide, including China, India and Europe. PLC technology monitors and drives hydroforming production and is being revamped to accommodate the new digital information flow on functionality to improve performance, margin and competitive position.
- Custom tube production. Alloy’s custom tube mills produce continuous-flow, thin-walled, seamed tubing for its proprietary bellows assemblies. Advanced seam tracking and arc control technologies help to ensure quality, consistency and a competitive advantage, while custom-designed, advanced laser tube cutting improves product throughput and reduces production costs. ●
In 1952, Bowden Manufacturing joined Northeast Ohio’s storied industrial footprint. As the company’s team and technologies have evolved, President Andrew McCartney has been at the forefront of growth and innovation. The company continues to help lead the manufacturing industry with innovative approaches that create jobs and integrate robotics into everyday functions without losing the human element of craftsmanship.
Bowden is part of the resurgent domestic manufacturing supply base. Its vision is to consistently provide a level of service and

President
relationships that help customers feel like they have their own in-house CNC shop — but with the expertise and manufacturing horsepower of a larger supplier. The company remains committed to exceptional communication and transparency throughout the manufacturing process. And internally, Bowden is developing its Next Generation of Manufacturing Professionals and Design Engineers, designed to lead the company and community for decades to come. This combats the trend in recent years in which staffing in all sectors has become extremely challenging, an areas that was already particularly difficult before the current constraints in manufacturing, partly as a result of continued exposure to global competition.
Prior to the pandemic, Bowden had attempted to utilize automation. So with labor challenges and the growth of its Manufacturing Next Gen program, the company decided to give automated machine loading another try. Bowden has been excited to partner with MAGNET and Absolute Machine Tool to bring in a Fanuc robot to load two of its CNC vertical mills in an automated fashion.
As the team embraces automation to help meet production goals and continues to apply new methods to serve customers, Bowden is expanding its capabilities and creating future opportunities for its creative engineers. ●
Codonics is an ISO 13485-certified, Food and Drug Administration-registered innovator and manufacturer of FDA-listed medical devices. The company’s primary focus is the development, manufacture and sale of its FDA Class II medical device product line. However, in recent years, Codonics expanded its capabilities to include contract manufacturing of other Original Equipment Manufacturer (OEM) products.
Although these products are not medical devices, the company utilizes the same high quality and control required to produce its Class II medical devices. This enables the OEMs to benefit from ISO 13485- and FDA-compliant manufacturing.
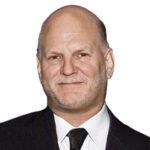
President and CEO
Codonics U.S.A. medical devices are sold worldwide and can be found throughout hospitals in modalities that include radiology for diagnostic imaging, perioperative and procedural settings, and patient safety solutions that help reduce preventable errors. Codonics Greater China’s manufacturing facility also produces consumable products sold in-country to its medical device customers.
Like many companies, Codonics has faced post-pandemic uncertainty and labor challenges. However, under the leadership of President and CEO Peter Botten, its mission is as relevant as ever. The company has successfully maintained employment levels through a combination of highly competitive wages and flexibility for its staff. A lean, adaptive workforce has enabled it to balance the demands of its internal product lines with OEM contract manufacturing. Additionally, operations and engineering teams have overcome challenges with parts availability and lead times.
Today, Codonics is represented in 110 countries, maintains offices in the U.S., France and China, and has more than 60,000 medical device installations. Looking to the future, the company continues to seek out innovations that will drive the next generations of products and business opportunities. ●
Enterprise Welding & Fabricating Inc. has been in business for almost five decades.
Founded in 1975 by brothers Ivan and Slavko Katic, the family-owned company has earned a reputation for providing prompt, real-world solutions for superior production and new product development. Now led by President Mike Katic, Enterprise Welding specializes in metal fabrication and supply for many premier Original Equipment Manufacturer (OEM) customers.
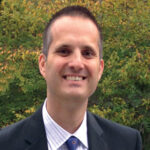
President
The organization is made up of a professional team utilizing world-class manufacturing techniques with industry-leading and innovative equipment. From fiber optic lasers to robotic welding, Enterprise Welding uses automated equipment to serve its partners in agriculture, construction, transportation, material handling, medical and defense sectors. Always striving for perfection, the motto “Right the first time and every time” is the foundation for Enterprise’s relentless pursuit of production consistency.
In addition to superior robotic and manual Gas Metal Arc Welding, Enterprise’s expertise includes laser-cutting, Computer Numerically Controlled punching, forming and machining, resistance welding and Class A industrial powder painting. Customers rely on Enterprise to produce parts that are welded to code, including safety-critical components. The company supports multiple locations with an uninterrupted supply of spec-perfect production-line parts. Enterprise’s innovative manufacturing techniques and engineering creativity also offer cost savings to its clients.
Located in Mentor, Ohio, Enterprise utilizes 182,000 square feet and state-of-the-art equipment for its product assembly lines, where more than 125 dedicated employees produce components for world-class customers. Both cellular and batch-build systems optimize throughput to maximize quality and productivity. Additionally, the company’s experienced engineers work with customers’ design teams to tailor the manufacturing process around critical part details. ●
Founded in 2002, Keene Building Products owns and operates several companies specializing in manufacturing and distributing high-quality building materials, custom specialty paint, resinous floor coatings, 3D printing filament and thermoplastic welding rod.
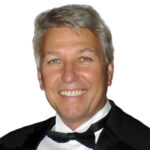
Owner
Led by Owner James Keene, the company covers commercial, residential and multi-family systems and has utility in many construction applications. The most important factors in the evolution of Keene are automation and scale — key contributors that have enabled the company’s growth over the past decade. Automation has limited the number of people required to manage operations and facilitated the 10-fold increase in company size since 2013.
Located in Euclid, Ohio, Keene Building Products has updated its facility through incremental improvements. A 42,000-square-foot facility acquired in 2014 was only partially needed at the time. Today, Keene occupies almost 100,000 square feet through new construction and utilization of outlying buildings that came with the original acquisition.
Equipment automation has been a continuous process. Since the company’s founding, three iterations of plastic geometric molding systems have been installed. The current version is allowing for the fastest production time and widest width production in North America for the manufacture of structured strand, the filament-based roll product Keene is known for producing. The company is the largest manufacturer of structured strand and has overtaken other Fortune 500 companies to achieve the dominant market share. Structured strand products are useful in roofing, wall construction, foundations and flooring. The application exemplifies Keene’s ability to add to its capabilities.
While the company has acquired or started nine entities over the years, 85 percent of its business has been organically generated. ●
North American Coating Laboratories (NACL) provides thin-film coatings for polymer and glass optical markets. The company’s experience in both dip and vacuum-applied processes has made NACL one of the most respected organizations in the optical coatings industry since its founding in 1974.
Led by President and CEO Brian Wilson, NACL consistently demonstrates a commitment to evolving manufacturing operations in the domestic and international marketplace.
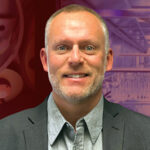
President and CEO
Embodying the spirit of its motto, “Here to Help,” NACL team members recognize the need for adaptability and superior service to address the evolving demands of the global economy.
NACL is forward-thinking, looking for ways to outpace the competition and bring added value and service to customers. While the industry typically relies on third-party shops to make the tooling and fixtures properly hold optics during the coating and cleaning process, NACL saw an opportunity to bring all tooling needs in-house to cut costs and lead times and pass savings to its customers. Further, the adoption of 3D printing for prototyping provides the ability to confirm how the company will handle customer parts when they arrive, saving additional time, money and engineering efforts.
Utilizing Google, Semrush — an SEO and competitor analysis tool — and trade resources, the NACL team recognized the opportunity for growth within the European market. The decision to open a sales office in Europe reflects the company’s proactive approach to meeting the growing demand for optical coating overseas.
This expansion has allowed the organization to better connect its domestic technical team to new markets of potential customers by offering localized sales and customer support. ●
Founded in 1990 by Adam DeFranceso and headquartered in Cleveland, Ohio, OMNI Systems is the largest privately owned label converter in the U.S. The company provides thermal label solutions, including direct thermal labels, thermal transfer labels, barcode labels, prime/merchandising labels, ribbons and more across various industries for companies of every size. Through the years, OMNI Systems has expanded its portfolio from secondary labels to a top-tier primary label supplier for Fortune 500 companies.

President and COO
Led by President and COO Michael Murton, the company continues its success by focusing on its core strength: supplying clients that have high-volume labeling requirements and a need for uncompromising quality, fulfillment, delivery and service. OMNI is now one of the largest consumers of thermal media from the nation’s leading raw material suppliers. This purchasing power allows the company to procure the highest quality raw material components at the lowest prices to meet the needs of its customers.
OMNI has grown its business organically over the past 32 years through a relentless focus on its mission, vision and values. Over the past decade, the company has achieved consistent, sustainable, double-digit growth in an industry that grows an average of 2 to 3 percent annually. There has been a dramatic shift in profitability improvement by nearly 150 percent with similar revenue numbers in recent years. Key strategies that have helped achieve these results include operational cadence and data-driven decision-making.
OMNI recognizes that, beyond the investment in its people, everything starts with understanding performance. The ability to dig deep into the analytics of each machine, item and order helps ensure the company is performing at an optimum level. ●
Before Jennifer Ake-Marriott took over as CEO, Redmond Waltz Electric was a struggling small business, limping forward day to day and on the precipice of closing its doors. There was distrust among workers and vendors, the electric motor service and repair company was sinking into debt and turnover was at an all-time high. The environment was unstable and unsustainable.
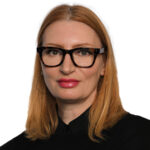
CEO
Redmond Waltz Electric needed a major transformation, and Ake-Marriott was the chosen leader and disruptor to begin anew. A decade later, she is viewed as an empathic leader who has made an indelible mark on her company and its employees.
Ake-Marriott became personally involved from day one. She conducted in-depth interviews with her employees, vendors and customers. Drawing on wisdom gained from years of management experience, she recognized the failings were not a result of just one person or circumstance. After a listening tour and an analysis of business operations, Ake-Marriott put her efforts into earning the trust of each employee, improving communication and streamlining operations. She made incremental changes and focused on building a culture of trust. Within two years, the company became profitable, vendor relationships were restored and revenue increased by almost 65 percent. Within five years, more than $1 million in debt had been retired.
Demonstrating she was a leader worth trusting, Ake-Marriott breathed new life into the company, leading to a transformative change that set Redmond Waltz on a new path for success. As a result, the 77-year-old Cleveland industrial repair company has been recognized in the community with honors and awards, and Ake-Marriott is noted as a thought leader in her industry. ●
Stakes Manufacturing LLC is a global leader in the print-on-demand apparel and accessory industry, specializing in retail-quality clothing, bags and hats for sports, entertainment, retail and e-commerce customers.
Led by Co-founders Jed Seifert and Vince Bartozzi, the company has invested in technology, automation and AI to adapt to the global economy. Stakes Manufacturing has also invested in its core team to create strong career paths and build deep roots to execute its mission and vision. Seifert, Bartozzi and their team look at advancements in automation and AI to complement their core team and improve efficiency, which ultimately benefits Stakes’ clients and customers.
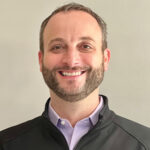
Co-founder
To compete against near-shore competition with labor with labor that is 80 percent less expensive, Stakes 80 percent less expensive labor, Stakes is utilizing automation and AI to offer nearly 120,000 individual SKUs to clients, whereas its competitors offer only 5,000. Stakes is committed to speed, quality and an extensive material catalog and has developed a comprehensive supply chain platform with 48-hour turnaround times.
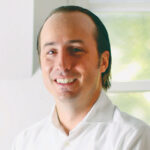
Co-founder
Team members accept each order, procure the blank garment, receive, warehouse, pick and stage the garment, print the garment, complete quality control checks and fulfill the final product directly to customers within 48 hours.
Stakes operates digital print technology that is far more environmentally friendly than that of traditional screen printing. Its equipment meets the highest sustainability standards, produces zero wastewater, has a low carbon footprint and utilizes an energy-saving process for eco-friendly consumers.
Looking ahead, the company continues to scale production to meet the capacity needs of its partners, working collaboratively to forecast current needs and ensure future production capacity. ●
Talan Products is a full-service metal stamping company and manufacturer of tooling and engineered parts. The company, led by CEO Steve Peplin, serves more than 150 customers in the fastener, building products, appliance, hardware, defense and transportation markets. Since incorporating in 1986, Talan Products has become one of the most acclaimed and highly regarded stampers in the U.S.
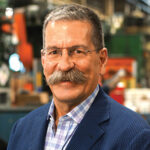
CEO
In the face of ongoing challenges in the manufacturing industry, the company has demonstrated exceptional innovation and adaptability, particularly in addressing the critical aspects of equipment, raw materials and labor. Talan Products has proactively addressed the challenges posed by the scarcity of raw materials in recent years by investing strategically in equipment, adding three new robot welding cells, an automated stud welding cell, a large automated cell for extrusion fabrication and three powerful punch presses.
This foresight has allowed Peplin and Talan Products to maintain production efficiency during material shortages and position itself as a reliable manufacturer for its customers. While achieving significant growth from 2021 to 2022, Talan was able to meet customer demands with on-time deliveries and very few customer quality concerns.
Recognizing the importance of skilled labor in its operations, Talan Products identified the need for a proactive and sustainable solution. In response to the need for skilled labor, the company launched Talan U, an internal educational program aimed at addressing the skills gap in manufacturing and upskilling its team members. Implementing Talan U has enhanced the team and fostered a positive and inclusive company culture.
The company’s commitment to developing the next generation of manufacturers aligns with its impressive 18.7 percent compound annual growth rate over the past 37 years. ●
Victoriaville & Co. is the third-largest manufacturer of wooden caskets in North America and one of the most important distributors of funeral products. Founded in 1907 and committed exclusively to the funeral industry since 1948, the fourth-generation family business is now led by Executive Vice President and COO Charles-Oliver Dumont.
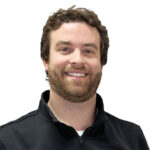
Executive vice president and COO
Victoriaville & Co. continually looks for new methods, processes and tools to meet and exceed its customers’ ever-increasing expectations. In 2023, the company embarked on its third manufacturing facility, announcing its investment in the construction of a 67,000-square-foot building in Cleveland, Ohio. This facility will allow Victoriaville & Co. to expand its capacity and respond more quickly to its growing customer base across the United States. Additionally, the project will create jobs for 70 to 100 teammates and be built with the purchase of components from the local supply base throughout Northeast Ohio.
Utilizing lean manufacturing techniques, the company’s state-of-the-art layout and sophisticated enterprise resource planning (ERP) tools, Dumont and his team will be able to manufacture and ship an order in one-third the time of their competition. Victoriaville is responding to customers’ demands to hold less inventory and promptly support families in their time of need.
Advanced manufacturing techniques and automation have decreased the company’s hours per unit to industry-leading levels, enabling Victoriaville to remain price-competitive in the global marketplace. Ohio has the highest percentage of family-owned funeral homes in the U.S. and, as it continues to expand, the company is committed to bringing manufacturing back to Northeast Ohio and meeting the needs of funeral homes and families in an unprecedented fashion. ●
Led by Co-founder and CEO Avery Hong, Zoetic Global’s mission is to revolutionize the energy sector through innovative solutions that unleash the power of renewable resources. With passion and purpose, the company creates a sustainable future, empowering communities and driving global progress toward a cleaner, greener planet.
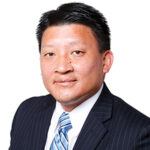
Co-founder and CEO
Over the past decade, Zoetic Global has undergone a transformative journey in its operations. Embracing cutting-edge industry technology, the company has integrated environmental solutions that are innovative, impactful, immediate and investable into all aspects of its business platform. This has enhanced efficiency and allowed the company to be more agile in responding to worldwide market demands. Zoetic Global’s products create a go-forward strategy for its partners, helping the environment today while transitioning into the future.
Navigating the challenges posed by the dynamic global economy, Zoetic Global has strategically diversified its portfolio of elite technologies in energy efficiency and generation of water purification. By establishing a resilient, globally dispersed network, the company has mitigated the risks associated with geopolitical uncertainties, trade fluctuations and disruptions caused by unforeseen events. Additionally, its proactive approach to embracing emerging technologies has improved operational efficiency and positioned the company as a trailblazer in the industry.
During its growth trajectory, Zoetic Global has encountered challenges inherent to expansion. These challenges include scaling production capacity, maintaining product innovation and optimizing supply chain logistics. The company has implemented rigorous quality control measures, invested in workforce training programs and leveraged advanced forecasting models to streamline its supply chain.
Zoetic Global continues to focus on market-ready solutions that can rapidly scale, making a significant impact in today’s world. ●