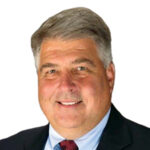
Alliance Industrial Solutions is again proud to be the presenting sponsor for the 2022 Evolution of Manufacturing awards. While we all hoped that 2021 would bring us closer to normal, we’ve faced continued challenges — navigating safety in the workplace, staying competitive with rising pay rates, managing through the Great Resignation, and ultimately, ensuring we have the right staff to keep production moving. In the face of these evolving and demanding times, it is important to recognize and celebrate the innovative ideas that companies bring to Northeast Ohio.
In many ways, this year’s honorees represent not only an evolution but also a transformation into the digital age, where flexibility and agility reign supreme. The manufacturing industry is expected to experience some major trends in 2022 that, if leveraged correctly, can fuel innovation and help businesses stay competitive. Some of these trends include AI and analytics, automation becoming more accessible, robots, supply chain nearshoring and digital transformation. As manufacturers evolve and adapt to these new innovations, our workforces will need to change, as well.
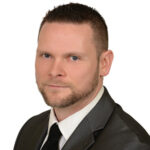
We have to stay at the forefront of this rapid change for so many reasons, the biggest being the impact on talent. Automation doesn’t eliminate the need for workers; it changes the skills those workers need, as well as the talent marketplace where we compete. Manufacturing remains just a single choice out of myriad options — how are we ensuring that our businesses are the ones they choose?
Our goal is to work with every company in Northeast Ohio that values talent as their most important resource. That’s what workers want, too — to be appreciated and feel like they are making a difference. A career in manufacturing can be more exciting and rewarding than ever. Our honorees make that abundantly clear.
Congratulations to all of this year’s winners for making their mark on manufacturing, and specifically for choosing Northeast Ohio as their place to evolve and make their magic happen. ●
2022 Award Honorees

Founded in 1940 in Cleveland, Ohio, AT&F Advanced Metals has grown to become a preferred supplier of metal supply, fabrications and services that push the limits of thickness, scale and precision. As a world-class metal fabricator, AT&F fabricates metals for some of the world’s greatest feats of engineering.
Led by President and CEO Michael Ripich, operations delve into materials processing and components for the industrial, energy and defense industries — one of which was the proposed wind turbines in Lake Erie, which ultimately did not move forward. AT&F works with stainless steel and exotic alloy fabrication for corrosive environments, as well as metallic and composite armor technology for military use. This work is found on submarines and aircraft carriers, at construction sites and mining operations, in labs and refineries, in rail cars and armored vehicles, and nearly anywhere a complex steel fabrication exists.
AT&F is more than just a steel-processing service center that provides materials, steel fabrication, component manufacturing and assemblies. The company’s passion to drive innovation inspires its team members to deliver best-in-class solutions and exceptional service to a wide range of heavy industrial manufacturers — a responsibility that requires outside-the-box thinking and the desire to evolve the process.
This ongoing mission to innovate in order to build, protect, energize and move the world has impacted the way the company protects the men and women who serve this country. Whether on land or sea, AT&F’s contribution to steel fabrication is there to serve those who serve.
This growth and innovation are by no means an accident. AT&F relies on its “Three Uniques” that set it apart from the competition and make AT&F desirable for strategic partnership — industry-leading reliability, data-driven management systems and more than 80 years of innovation and investment. ●
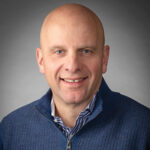
In 2021, Eaton took significant steps to strengthen the sustainability and resilience of its operations throughout the world, including its recently announced microgrid projects at two of its manufacturing facilities in Puerto Rico. Michael Regelski, senior vice president, R&D – Intelligent Power Solutions and chief technology officer, Electrical Sector, leading the charge, microgrid systems are being installed at Eaton manufacturing plants in the Arecibo and Las Piedras facilities that will contribute a combined 10 MWac of solar PV and 2.23 MW/4.46 MWh of battery storage in Puerto Rico. This will reduce emissions by limiting the need for carbon-intensive electricity during peak demand periods. The two microgrids will enable these plants to reduce emissions by 8,345 metric tons in the first year of operation.
Both systems will be built to withstand a Category 5 hurricane, helping to ensure continuity of operations and relieve overtaxing of local systems during times of climate emergency. These projects demonstrate Eaton’s focus on accelerating the energy transition and helping customers and communities unlock a low-carbon energy future.
Around the world, Eaton is applying its Everything as a Grid approach to strengthen operations with low-carbon energy sources and the ability to withstand extreme weather emergencies. Partnering with Enel X, it has established a replicable energy-as-a-service model that exemplifies how to keep the power on — no matter what.
Microgrid systems help prepare for the unexpected by balancing where, when and how electricity is consumed to improve resilience, including during grid outage events. They also provide added value when grid conditions are normal by generating renewable energy from the solar panels, which can be consumed, or stored and delivered back to the local grid to reduce stress on regional utility infrastructure.
As extreme weather caused by the climate crisis becomes the new normal, commercial and industrial businesses need to adopt an integrated energy strategy and solutions that are both resilient and sustainable. ●
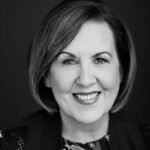
Exsurco Medical is a leading-edge device manufacturer of products for tissue banks and professionals. Committed to advancing excision science, Exsurco Medical manufactures devices to help professionals improve the lives of patients in need of the healing power of skin.
Based in Wakeman, Ohio, and led by President Sara Ann MacKinlay, the facility houses all production and operations. Vertically integrated and equipped with a Class 7 cleanroom for assembly and packaging, it allows for warehousing of finished goods and corporate offices to service customers at one site. Exsurco Medical is an ISO 13485 certified company and an FDA registered medical device company.
From the ground up, Exsurco Medical engineered the Amalgatome® MD and the Amalgatome® SK — a leap forward in tissue removal technology that allows technicians to work faster and recover higher yields. The result is that donated skin and tissue heals more wounds, restores patient confidence and contributes to groundbreaking research.
Exsurco continues to redefine excision science with Amalgatome MD, an innovative skin recovery product. Designed specifically for use in tissue banks, the unique rotary design allows technicians to maneuver over body contours and hard-to-reach areas that are challenging for standard allograft recovery techniques.
Amalgatome SK, a full thickness tissue processing product, was developed to improve the process of removing adipose tissue from a full-thickness allograft donor. Its advanced and ergonomic design delivers comfort during use, while providing an effective and efficient solution to the technician for producing high-quality, full-thickness skin grafts. Both products are available for cadaveric use only.
In addition, Exsurco Medical’s innovative and proprietary excision design is a critical step in launching the company’s new surgical device for health care professionals. The Amalgatome® SD skin grafting and wound debridement device is available for use in the operating room for burn and trauma patients. ●
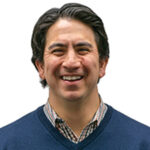
Since 1949, G&S Metal Products Company Inc. has grown to become the largest producer of metal bakeware in the United States. For a company to survive and prosper for more than 70 years, the founding principles must be strong, and the company must be committed to change. G&S Metal Products was established on the basic principles of delivering a quality product at a reasonable price with unparalleled customer service. It sounds simple, but adapting to a global economy has meant that G&S has evolved into being a vertically integrated company, starting with purchasing its own raw material from the nation’s largest and best steel mills. The company then added a coil coating operation into its Hamden, Connecticut, facility. After the nonstick finish is applied there, the product is then shipped to the company’s Cleveland, Ohio, headquarters for inspection, stamping, packaging and distribution. G&S Metal Products also had the foresight to expand with offices in Asia, allowing access to partner suppliers for household and kitchen gadgets.
The business continues to grow by expanding its product line and its customer base. Listening to the customer allows the company to bring new and improved products to market, all while following the principles of providing quality products at a reasonable price. Since the start of the pandemic, the company has prospered significantly with the increased interest in in-home cooking, as G&S was able to meet the increase in demand due to its vertically integrated structure.
Led by President Chris Schwartz, G&S has benefited from a philosophy of tenured relationships. These start with the employees and are present throughout all levels of the organization, including suppliers, service firms and customers. As a new generation of leaders takes the helm at the company, G&S has ensured its longevity and ongoing success. ●
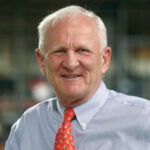
In 1942, Jack Schron Sr. founded Glenn Tool and Manufacturing with his father, Christy. In response to the needs of wartime production, they began to manufacture standard components, with the goal of helping American manufacturers operate quickly and more efficiently. “The Standard Components with the Highest Standards” became this company’s founding philosophy, and it put Jergens Inc. on the forefront of the lean manufacturing movement.
The Jergens Manufacturing Campus in Cleveland, Ohio, is built on a 47-acre site, formerly an abandoned rail yard, the result of Jergens’ commitment to sustainability and urban renewal.
Today, led by President Jack Schron, the company has grown and is composed of three distinct business units: Workholding Solutions, Lifting Solutions and Specialty Fasteners. Building on its reputation for uncompromising quality standards, it is committed to helping customers achieve leaner, more profitable manufacturing, and the company continues to add products and engineered solutions for an integrated approach to “Manufacturing Efficiency.”
Jergens’ tooling components, fasteners and hoist rings are at work in just about every industry on every continent, and its innovative engineered solutions have changed the way manufacturers worldwide think about productivity. The company manufactures more than 80 percent of what it sells in its 130,000-square-foot Cleveland facility, guaranteeing high-quality, competitive pricing and immediate availability.
In response to the pandemic, Jergens implemented an order priority initiative for all medical device manufacturers. It received a call from partner DMG Mori, stating that medical device manufacturer Vyaire Medical was in desperate need of parts to build ventilators.
The Jergens team traveled to the Vyaire facility to reverse engineer the company’s current tooling. Within three weeks, Jergens had reversed engineered its process, provided product drawings to the engineering team, fabricated and shipped custom tooling, installed the new setup and cutting chips, and implemented a custom workholding solution. ●
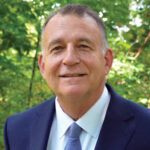
Growing consumer pressure and tightening governmental regulations are prompting a worldwide search for natural, environmentally friendly, nontoxic biological solutions to replace harsh synthetic chemicals. Biosurfactants have been studied for decades and validated as one of the most promising green ingredients, but costly manufacturing methods with limited volume capacity have restricted their use in key industries.
With Co-founder Andrew Lefkowitz at the helm, Locus Fermentation Solutions (Locus FS) has evolved its manufacturing operations to meet this global demand by developing ISO 9001-certified processes to create high-quality, non-GMO, 100 percent biobased biosurfactant ingredients produced with a near-zero carbon footprint. The company is continuously advancing its methods to produce these ESG-friendly ingredients with higher productivity at a fraction of the production time and cost of traditional fermentation processes.
Locus FS’ novel manufacturing process is protected by 39 patents and 19 trade secrets, and utilizes three key elements: bioinformatics, used to identify proven microbial strains with specific mechanisms of action that will produce biosurfactants with desired characteristics in the end-use application; modular fermentation, in which the company custom designs and builds its own fermenters for production capabilities with higher concentrations, shorter cycle times and less than 10 percent CAPEX of traditional fermenters; and purification, in which its energy-efficient downstream purification method uses no volatile solvents and ensures consistent purity, ease of formulation and compatibility with other ingredients.
The patented manufacturing process is rapidly scalable in less than a year and enables production of biosurfactants at the volumes and price points needed for widespread adoption across key industry sectors. The biosurfactants are USDA certified as 100 percent biobased and produced from renewable raw materials, providing ESG benefits coupled with unmatched multifunctionality and superior performance. This results in sustainable solutions that boost productivity, reduce unit cost, maximize compatibility and offer unmatched flexibility to match the demands of a rapidly evolving global economy. ●
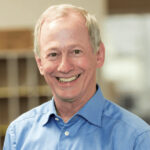
Led by President and CEO Peter Broer, Lumitex designs and develops new lighting systems using best-in-class techniques, practices, software modeling and quality systems to create innovative solutions and looks for new and existing lighting systems. The company serves highly regulated markets such as phototherapy, automotive, surgical and aerospace, and it reduces its customers’ infrastructure and overhead needs for testing, compliance and regulation.
For example, in the medical field, customers are looking to optimize light in medical products. However, lighting design is complex, and it isn’t easy to deliver light in exactly the right way. In addition, hiring optical engineers is expensive, navigating the extensive lighting landscape is challenging and internal resources are often limited.
That’s where Lumitex comes in, providing everything its customers need to develop lighting for their medical products to improve the standard of care. This allows them to stop relying on trial and error development processes and leverage Lumitex’s experts to streamline their approach to lighting and target light to help a product perform at its best.
The company uses an unbiased approach to technology selection to provide customers with the best solution for their needs, using technology from a variety of partners and suppliers. After development, Lumitex works with the customer to optimize the design for the most effective production method with the company and/or a third party.
With more than 30 years of experience helping medical product companies with lighting, today millions of patients depend on Lumitex lighting for their care. The company has succeeded because it doesn’t rely on off-the-shelf lighting solutions. Instead, its employees use their knowledge to help in the full lighting development process with customers, providing them with an unbiased use of technology, optical expertise, engineering and development expertise. It also provides design for manufacturing, expertise in highly regulated markets and cost-effective production and final assembly. ●
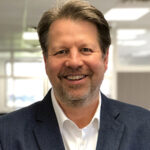
National Office is an office furniture manufacturer based in Cleveland, Ohio, that distributes its Gen2 Office Furniture product line to furniture dealers both throughout the United States and factory direct in Northeast Ohio.
As National Office enters its 55th year in business, it has been challenged with major issues affecting its manufacturing operations, primarily with materials and people. Since the start of the economic shutdown in early 2020, the company has experienced a larger impact on operations than any time previously. However, regardless of the issues, the company’s leadership knows it is critical to understand the situation, face it and then adjust.
With domestic and global supply chains in turmoil, every business is impacted. About 20 years ago, the company began importing steel components from China. The benefit was the lower cost of manufacturing, but with longer lead times, it realized it should not sole-source from Chinese suppliers.
That realization was a savior with the impact of the pandemic. For every imported item, National Office created domestic sources for the same products. As doing business with China became more costly, it was able to transition to viable domestic suppliers without delay, and the goal is to cease all manufacturing in China.
Over the past 10 years, the family business has transitioned ownership from the first generation to the second, which was completed in 2018. With Gregory Schneider at the helm as CEO, the transition also changed management styles, from more autocratic to more democratic. In addition to staff gaining more trust and responsibility, they received more flexibility with their work schedule and paid time off as the company acknowledged a balance between family life and work life. This has also created a more positive culture; retaining workers is more important than attracting new ones because, if you retain employees first, attracting new ones becomes easier. ●
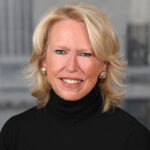
When Sarah Nash took over as chair, CEO and president in 2018, Novagard was a regional manufacturer of industrial-grade silicones mainly sold to the construction industry. Novagard also manufactured silicone greases and foam used primarily in the automotive market.
But the markets were changing, and Nash saw the broader role silicones could play in the manufacturing process. As the world became increasingly focused on the electrification of everything, more and more companies were looking for world-class protection of their critical components. Silicones — with their superior stability, durability and flexibility across broad temperature ranges — provide excellent insulation, vibration damping and barrier protection against weather and other intrusions in electronics applications.
Nash made the strategic decision to shift from an industrial-grade to an electronics-grade manufacturer of silicones. She began a multiyear, multimillion-dollar investment plan in Novagard’s people, plant and processes, focusing on R&D. That added technical expertise, and it began manufacturing specialty chemicals used in its proprietary formulations in 2019.
The company rolled out the industry’s broadest line of UV/dual cure silicones that move components to the next step of assembly in seconds rather than days, shaving valuable time off processing without compromising quality. Before Novagard could create a state-of-the-art production environment, it had to upgrade the electrical capacity in its more than 100-year-old building. With a facility-wide power upgrade, new substations and wiring in place, it added custom-built equipment and automated raw material handling and dispensing systems. Its operations team automated aspects of production and packaging, including SPC manufacturing data and in-process quality control, leading to a true manufacturing 4.0 environment.
But the success of these changes also relied on suppliers providing the raw materials necessary for Novagard’s manufacturing processes. Nash played a key role in stabilizing Novagard’s supply chain, solidifying long-term partnerships and strategic agreements and helping to secure transportation within the global logistics network. ●
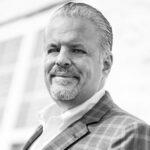
Orlando Baking Co. is a family organization founded in Castel di Sangro, Italy, in 1872 — and that original bakery is still in operation today. In 1904, some members of the founding family moved to Cleveland, Ohio, and re-established the Old World ways of baking European classics. One hundred fifty years later, led by President and CEO John Anthony Orlando, the family continues to provide product to both businesses and consumers.
Throughout the years, Orlando Baking Co. has continuously undergone expansion, leading to a state-of-the-art bakery on Cleveland’s near east side. After five generations, the family is proud to carry on the Orlando tradition of baking with high-quality, natural ingredients.
Orlando Baking produces more than 250 varieties of fresh and frozen hearth-baked breads, rolls and specialty items. Its product line includes Italian, French, rye and wheat breads; an extensive variety of subs, hoagies, kaisers and hamburger buns; and one of the largest varieties of dinner rolls offered by any bakery. Its signature Ciabatta bread is a staple on menus across America, as are its stone-baked artisan breads. In addition, the company is constantly expanding its product line and has recently added pretzel bread products.
Equipped with nine production lines, Orlando Baking’s 250,000-square-foot state-of-the-art facility uses the most modern baking equipment available to create Old World European taste and consistency. The company’s tunnel and stone hearth ovens are designed to accommodate product diversity and ensure consistency.
A blast freezer locks in flavor and freshness to provide Orlando customers with fresh-baked taste at their convenience. Its innovative Ciabatta line was the first line of its kind in the United States, and the Orlando Ciabatta process is unequaled in this country. By combining state-of-the-art technology with the finest ingredients, the organization is able to bake the most authentic and best-tasting specialty breads. ●
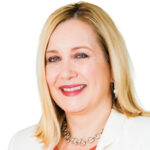
Always thinking about the future, Process Technology President Jodi Richards prepared for a potential shutdown by charging the HR, IT and Operations leads with developing worker safety implementation measures and flexible work-from-home options for eligible team members before COVID-19 hit.
This forward-thinking action allowed the company to activate the already-in-place plan for all locations immediately. Additionally, the COVID FMLA law allowed Process Technology — a global, U.S.-based company focused on designing and manufacturing world-class thermal and power supply products — to pay any sick or exposed team members full pay, which it voluntarily extended after the mandate ended. Through the global challenges of the last two years, Process Technology has increased both its sales and production, launched several new products, developed a new company website and delivered its most profitable year to date in 2021 — all while remaining committed to creating quality products that are safe, precise and clean for the industries it serves.
This exponential growth drove full-time staffing from 192 to 264 and led to the opening of a new production plant in Monterrey, Mexico. Additionally, the Mentor, Ohio, production facility fully remodeled its office space, and a new high-purity production area opened in the Willoughby, Ohio, location, allowing the company to produce products born out of collaboration and technological expertise.
Process Technology delivers innovative, eco-friendly, in-demand high-purity and surface finishing heaters, and power supplies and accessories for the semiconductor, aerospace, automotive, flat panel display, solar and medical device industries. The company is continuously improving its products and processes through advanced design, engineering, technology, digitization, production and training, and its technical experts are always ready to assist. In addition, its process technology team members are motivated at every step of the process to provide world-class service to its customers, working together to make Process Technology better every day. ●
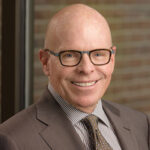
In 1949, Frank W. Steere Jr., a chemical engineer working for the BF Goodrich Co., started his own business around a new vinyl plastisol material he was introduced to in the rubber industry.
With less than $1,000, Steere set up shop in the basement of his Akron, Ohio, home. His father told him that, one day, through hard work, a picture of him working in the basement would be framed in his company’s lobby. Almost 70 years later, that picture is proudly displayed in the lobby.
Steere purchased used ovens and began coating various applications in the vinyl material. With a shortage of stainless steel in the market, he quickly saw a need to coat industrial bolts and called on the Industrial Rayon Corp. It was here that he made the first sale for STEERE Enterprises Inc. His first product, vinyl coated 3/8” hex bolts for Industrial Rayon, received positive feedback, and he received future purchase orders. As a result, Steere moved his operation out of the basement and into rented space in downtown Akron.
He then connected with Ben Stiller of Quikey Manufacturing Co. and began making dip molded, vinyl coin purses known as Quikoin — his first big success. In the 1950s, STEERE made over 50 million coin purses and expanded by selling vinyl grips and sleeves to other industries.
In the 1960s, STEERE started producing dip molded seat belt sleeves for the automotive market, and in 1962, the company built its headquarters in Tallmadge, Ohio, where it remains today.
In the 1970s, it began molding seat belt sleeves out of polyethylene, and in the 1980s, it produced blow molded air induction applications. In the 1990s, STEERE launched the patented DUAL PROCESS ™ overmolding.
Today, the company, led by Chairman and CEO Bill Steere, is a third-generation family-owned business. ●
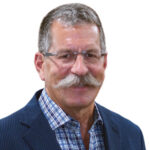
Talan Products Inc. has had to continue to evolve to remain a high-growth company for 35 years. It takes being on the cutting edge of your industry to have an 18 percent compound annual growth rate, and in 2022, the company is looking at a very healthy leap.
Onshoring — bringing manufacturing back to the U.S. from Asia — has been on the rise the last 10 years, a significant change to the $160 billion a year global market for metal stampings that Talan Products operates in. While Talan still had to compete with suppliers from Asia, it had to be a low-cost producer in the U.S.
To compete with other low-cost U.S. suppliers and low-cost Asian metal stampers, Talan focused on what makes it the best value supplier of its products. Buyers in the commercial marketplace are increasingly millennials, and in consumer buying, 83 percent of millennials make buying preferences with companies that align with their beliefs. That means in a heavy B2B environment, Talan must communicate its strong positive culture to be attractive to buyers bringing their personal habits into the B2B environment.
Talan Products has a strong, positive culture built on a commitment to safety, collaboration, tenacity/determination and respect. For many years, manufacturing was all about low price, and while that remains mostly the case, the industry is evolving to include the core values, beliefs and actions of industrial companies. As part of Talan’s evolution, it has recognized this and is utilizing it as part of its continued growth strategy.
Talan’s efficiency, measured by sales per employee, is at the top of its industry — more than three times the industry average. Led by CEO Steve Peplin, the company consistently monitors employee satisfaction with engagement surveys to ensure it remains an employer of choice. ●