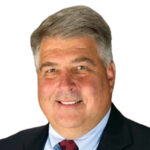
President, Alliance Industrial Solutions
Alliance Industrial Solutions is pleased to continue our presenting sponsorship of the Evolution of Manufacturing awards this year and celebrate local industry leaders. 2022 was undeniably eventful. The manufacturing industry experienced major trends that we predicted back in 2021: AI and analytics, more accessible automation, robots, supply chain nearshoring, and digital transformation. In true manufacturing spirit, we rolled up our sleeves and embraced these trends as they fueled innovation and helped companies stay competitive.
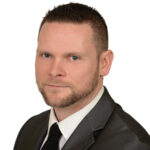
VP of Strategic Partnerships, Alliance Industrial Solutions
Output, hours worked, and production numbers finally recovered from COVID-19 — and continued to grow. The overall labor market navigated through “quiet quitting,” record-high inflation and rumblings of recession. It’s no surprise that manufacturing stepped up. This year’s honorees are proof of that. Despite most signs pointing to recession for months, we’ve not only kept manufacturing going, we’ve kept it growing. We survived a global pandemic, adapted and bounced back stronger than ever.
Today, the rumblings of recession are getting louder. So, in 2023, let last year’s progress fuel your growth in the face of an economic downturn. The best place to start? Investing in your talent. With the right people in place, there’s no limit to your company’s potential. Have open and honest dialogue with them. What are they seeing on the production floor that could be improved? Conduct stay interviews, pay them fairly, and make your teams feel valued and heard every day. With a fully charged workforce, you’ll maximize the impact every employee makes. You can bet your bottom line on it.
When it comes to recessions, it’s always a matter of when, not if. Economic highs and lows are an expected part of a free market economy, and we always land on our feet. If we’re lucky, we learn a few things along the way that help us become better employers — just like this year’s honorees.
Congratulations to this year’s winners for making their mark on manufacturing and growing their businesses in Northeast Ohio. ●
2023 Evolution Honorees
Founded in 1940 in Cleveland, Ohio, AT&F has grown to become a preferred supplier of metal supply, fabrications and services that push the limits of thickness, scale and precision.
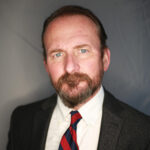
President
Operations delve into materials processing, components for industrial, and energy and defense industries — one of which being the proposed wind turbines in Lake Erie, which ultimately did not move forward. With Michael Ripich serving as president, AT&F works with stainless steel and exotic alloy fabrication for corrosive environments, as well as metallic and composite armor technology for military use. This work is found on submarines and aircraft carriers, at construction sites and mining operations, in labs and refineries, and nearly anywhere that a complex steel fabrication exists.
AT&F is more than just a steel-processing service center providing materials, steel fabrication, component manufacturing and assemblies. Its passion to drive innovation inspires team members to deliver best-in-class solutions and exceptional service to a wide range of heavy industrial manufacturers — a responsibility that requires outside-the-box thinking and the desire to evolve the process.
This ongoing mission to innovate in order to build, protect, energize and move the world has impacted the way the company protects the men and women who serve this country. Whether on land or sea, AT&F’s contribution to steel fabrication is there to serve those who serve.
This growth and innovation are by no means an accident. AT&F relies on its “Three Uniques” that set the company apart from competition and make it desirable for strategic partnership — industry-leading reliability, data-driven management system/“We Run on EOS” and more than 80 years of innovation and investment. ●
Bowden Manufacturing has evolved into one of the leading-edge users of Industry 4.0 technology applications among smaller manufacturers in Northeast Ohio. Starting in 2019, Bowden investigated what was then called IIoT (Industrial Internet of Things), beginning its journey to apply fresh technologies to enhance company operations, well ahead of most companies its size.
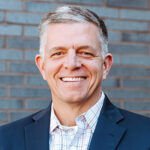
President
Bowden’s early adoption of the Machine Utilization Tracker (MUT) System provided increased visibility and productivity on the shop floor. Working directly with the MUT System developer Machine Tracking Inc., Bowden pioneered key enhancements to the system that are now available to other companies.
The first was the ability for the MUT System to set and display production targets for operators. This allows production supervisors opportunities to clearly establish expectations and track progress in real time during each shift. The other was the development of a Countdown Timer System to display the time remaining in the cycle of a machine in production. This system helps promote shop floor teamwork when running multiple machines as a group, using a centralized display of the time remaining on each machine. It provides advanced warning as the end of a production cycle is approaching to ensure they are in position to keep all their assigned machines running.
The real-time feedback from the machines to the displays allows for quicker investigation and troubleshooting when there are issues on the shop floor. Machines that are shown to be falling behind expectations early in a shift are more quickly identified and adjusted.
The team continues to be passionate about employing new technology to give American manufacturers the opportunity to compete positively on the world stage. Bowden is leading the way and routinely sharing its experience. ●
Brennan Industries has bought multi-tasking CNC machines, allowing one machine to do the job of two or three older machines and one person to run two or three of them. This also allows the company to buy round material and make the Hex sizes it needs itself, when the specific Hex sizes are unavailable to purchase.
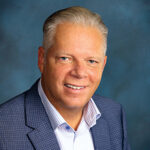
President and CEO
Led by President and CEO David Carr, Brennan Industries has instituted a lights-out program, in which an assigned person comes in on the weekends when the building is closed and within an hour can have three machines loaded and running production before going home. Machines will run for several hours unmanned with no one in the building. It also has second shift load the machines, for the night, allowing for more production off specific machines without the labor involved with running them.
In addition, the company became AS9100 certified to allow it to make aerospace fittings which it furnishes to SpaceX, Boeing, Bell and others. The changes have impacted operations, employment, product mix and sales by allowing Brennan to be adaptive with lack of material availability. And with the lack of eligible machinist candidates, it now has one person doing what four or more people did before as a result of its multi-tasking machines, allowing it to increase production and product mix, and increase shipping sales by 22 percent.
Finally, Brennan Industries has been putting a strong focus on manufacturing and will continue to do so through investments in new machines and recruiting top talent. ●
Cres Cor was established in 1936 as a job shop and during World War II was known for military products. After the war ended, the nation saw tremendous growth in restaurant dining, and the demand to keep delivered food products warm created a new market. Cres Cor’s two large customers were Hough Bakery and Colonel Sanders’ Kentucky Fried Chicken, and it grew to worldwide recognition for high-end food-warming cabinets, ovens and racks, with accurate temperature and humidity controls.
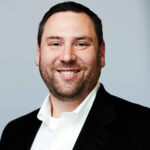
President
In early 2020, at the start of the pandemic, there was an initial shortage of personal protective masks, prompting the desire to decontaminate masks. Management at Cres Cor, led by President Greg Baggott, saw an opportunity to use its unique heating technology to clean the masks without chemicals.
After initial testing courtesy of University Hospitals of Cleveland, it was discovered that the cabinet heating technology was effective in decontaminating items, including masks. Cres Cor applied for Emergency Use Authorization through the FDA; shortly afterward, the supply chain of disposable masks caught up and the need to decontaminate used masks waned. Management discussed other options, and third-party laboratory testing confirmed the cabinets are an effective method for quickly disinfecting first responder gear used by firefighters, police and the military. To help protect first responders, Cres Guard and the Cres Cor Health & Safety division were established. COVID put a laser-like focus on the lack of a reliable and fast method of decontaminating responders’ gear, helmets, gloves and equipment bags.
The Cres Guard mobile decontamination cabinet utilizes heat and humidity in a 15-minute cycle to clean gear from biological hazards. ●
General Die Casters, Inc. is an early adopter of manufacturing technology and strives to find methods of integrating technologies to amplify their impact. The company is one of the first die casters to integrate plantwide process monitoring into its equipment.
Led by CEO Brian Lennon, General Die Casters integrated this into its automation to remove potentially defective castings from the process without involvement of a person. This data is automatically fed into the ERP system to provide additional data that can be used to gauge the performance of the organization and push continuous improvement.
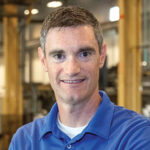
CEO
Industry 4.0 is well under way at the company, allowing it to produce some of the most technically challenging aluminum castings available today with world-class quality. Its offshore competition simply cannot match its quality and engineering capabilities.
In addition, educating and developing its workforce is one of the keys to success at General Die Casters. It continues to expand General Die Casters University, its internal education system, with classes specific to high-pressure die casting production and engineering, as well as precision CNC machining. This is one of the centerpieces of the company’s culture, which is centered on safety, education, empowerment and respect.
These changes have allowed the company to continuously grow sales 30 percent since before COVID without an increase in the amount of labor. The changes position the company to produce new casting designs that others are not capable of producing. As new product designs become more complex and the demand for domestic manufacturing increases, General Die Casters is in a solid position for growth. ●
Giesecke+Devrient is a global company that offers security technologies, both in the physical and digital world. Every day, billions of people benefit from G+D innovations in their personal and business lives. With about 11,600 employees across 32 countries, the company develops, manufactures and distributes products and solutions for the safeguarding of payment processes, identities, connectivity and data.
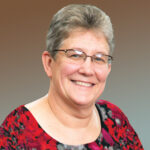
Vice president, Operations
It began in 1852, when the printing of securities started in Leipzig. Today, the company’s portfolio is as diverse as modern, mobile life. Anyone who pays by cash, card or smartphone is highly likely to be using the company’s technologies. There is one common goal behind all of these facets: Creating confidence, which G+D innovations does with four business sectors: G+D Currency Technology, G+D Mobile Security, Veridos (a joint venture with Bundesdruckerei), and secunet.
G+D has been the trusted partner of the most demanding institutions since 1852. Today, its goal is to shape trust in a digital world without changing what it always did: Creating confidence. It engineers customized security technologies with passion and precision in payment, connectivity, identities and digital infrastructures.
With Anne Markle serving as vice president, operations, the company secures payments across all physical, electronic and digital forms. As a true global market leader, more than 150 central banks and over 2,400 commercial banks, as well as all major payment schemes worldwide, trust its expertise. In securing cash payments, its portfolio caters for every stage in the lifecycle of a banknote. With G+D Filia®, it also provides applications for central banks to issue, distribute and monitor a digital form of cash — a Central Bank Digital Currency. ●
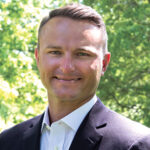
Kent Elastomer Products, Inc. began practicing LEAN manufacturing in 2006. It was reactive to situations, never changing the culture to be prepared for any given situation. Now it is quick and nimble, ready to respond to changes, problems and more with clarity and strategy.
It took a few years, but once Kent Elastomer Products thoroughly established these best practices in its three manufacturing and assembly facilities, it expanded its LEAN philosophy to other aspects of its business, continuing to improve sales and customer service best practices. It knew that for LEAN to work, it needed to be implemented in all areas of the company.
From an investment and resource perspective, the company has maintained its organizational philosophy to significantly grow the business and stay ahead of the competition by innovating its manufacturing operations.
Investments include implementation of a ISO13485 medical device quality system; installation of new air conditioning in Mogadore, assembly and automation equipment in Winesburg; and completion of the Kent office expansion and new training facilities. It has also developed a new latex tubing compound for the speargun market, partnering and co-developing a new tungsten polyisoprene attenuation glove recipe; purchased and commissioned a realer for added tubing/packaging capability; implemented scan and track barcode system companywide; and developed a fluid transfer tube and earned BPOG Test Package to meet standards of the biopharma industry.
These investments have provided efficiency gains while growing the business and bringing new technologies to market through its R&D efforts. ●
The immediate need for solutions that reduce the global carbon footprint has never been more urgent. High demand exists for biological solutions to replace chemicals in almost every industry, but manufacturing limitations, high costs and inconsistent performance have hindered adoption.
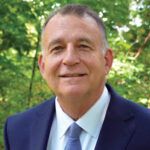
Founder, Chairman and CEO
Locus Fermentation Solutions has evolved its manufacturing operations to meet this global demand by developing carbon-neutral biomanufacturing that enables the cost-effective replacement of global chemical use. Protected by more than 1,200 patents valued at over $500 million, the novel approach transforms biologicals into green solutions that outperform alternatives in results, cost and sustainability.
Locus’ biomanufacturing process starts with combining renewable agricultural raw materials with specifically selected microorganisms like the probiotics taken for gut health. Through a unique microbrewery fermentation process similar to that of making beer, it transforms them into high-quality, palm-oil-free biologicals produced with a near-zero carbon footprint. They are also USDA BioPreferred certified as 100 percent biobased. Each one is tailored to address key ESG challenges in chemical-reliant industries.
The patented manufacturing process is rapidly scalable in less than a year and enables production of biologicals at the volumes and price points needed for widespread adoption across key industry sectors.
Locus is continuously advancing its methods to produce these ESG-friendly ingredients with higher productivity at a fraction of the production time and cost of traditional fermentation processes. It also expanded its facilities and secured a new manufacturing center in Solon that will more than triple its monthly production capacity, and its previous ISO-9001 certification was expanded to all production and quality-related functions. ●
Malco Products Inc. began in Barberton, Ohio, as a family-owned and operated specialty cleaning products company. Since 1953, Malco has grown into a global manufacturing company with a proprietary, on-site R&D lab and three world-class production facilities in Akron, Alliance and Barberton that manufacture specialty chemical products for the professional automotive, marine, aviation and industrial customer, operating multiple lines of business and serving customers in over 70 countries.
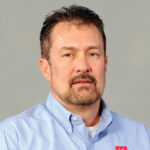
Vice president of Operations
Malco Products is no stranger to adaptation. In fact, the only way it has survived for 70 years as a strong manufacturing corporation is to embrace change. As a specialty chemical manufacturer, it has pivoted operations numerous times to meet the global market demand and ever-changing needs of customers and employees.
Malco’s quality management team drives a vigorous QIT (Quality Improvement Team) process with adaptive systems and processes that are built for continuous change. Employees are trained in problem-solving and encouraged to participate. Three times per year, natural and cross-functional teams report their project results to the executive leadership and their peers. In place since 1996, this QIT process continues to yield improvements and savings for Malco and its customers.
Robust quality management systems drive a continuous improvement culture at Malco to ensure product quality. Its ISO modeled systems are the product of implementing best-in-class practices gleaned from very rigorous audits performed regularly by world-class customers.
During the pandemic, Malco Products was an essential business and increased production, sales, growth and employment to keep up with demand. It employed creative tactics to attain, attract and hire new talent and supported international customers through virtual meetings, trainings and shipments of disinfectant products it produced in house. ●
OMNI Systems had primarily been focused on secondary labels — those used for supporting the movement of product through a company supply chain — when they had a new idea to expand into the prime label market. In comparison with secondary labels, prime labels help sell products and are used to gain consumers’ attention and make them want to buy a product.
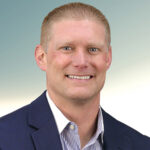
President and COO
In late 2021, a vision on OMNI Systems expanding into prime labels was presented. The expansion of its product offerings would support growing market share with current customers and help attract new customers. To differentiate from the competition, it was suggested that OMNI Systems focus on the larger prime orders, which would align with OMNI’s current manufacturing strategies. OMNI’s manufacturing strategies for 30-plus years have been to optimize paper widths, utilize automation throughout the process and maximize run speeds to keep production costs low, which has allowed it to provide labels at the lowest cost with the highest quality.
In early 2022, OMNI partnered with Mark Andy to purchase two 20-inch P7 printing presses with automation on both the input and output side of the press. OMNI added inline inspection capabilities with a vision system that inspects labels as they are being produced on the press. OMNI will be one of the few converters in the prime label space that has the capability to handle 20-inch-wide paper and invested in the in-line inspection system.
OMNI is in process of being validated as a prime label supplier for one of largest poultry producers in the U.S., and in 2023 plans to purchase an additional printing press to allow for additional prime label capacity and capability. ●
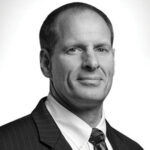
SIFCO Industries has built its 109-year legacy on the production of highly engineered forged components and product solutions for the aerospace, energy and defense markets. While SIFCO’s business remained strong during the height of the COVID pandemic, the related commercial aerospace downturn, Boeing’s company struggles and delays in the introduction of new military platforms forced it to adapt its value proposition to capitalize on new growth markets, products and customers.
Over the past two years, SIFCO has successfully entered the quickly growing commercial space and semiconductor market segments. It has capitalized on its technical knowledge and wide range of operational capabilities to achieve unique customer-specified metallurgical properties through a variety of forging operations and thermal cycles.
Customers depend upon its finite element analysis-driven design for tooling and processes. SIFCO’s cross-trained, flexible workforce and SAP change and capacity management systems, combined with its core values, are critical to succeeding, with both low- and high-volume products for these highly dynamic markets. At SIFCO, employees strive to deliver “Good Parts, On-time” and pride themselves on thriving in development and production environments.
While working to capitalize on technical core competencies to enter new markets, SIFCO has also remained dedicated to serving a growing global customer base. Roughly 30 percent of the sales from SIFCO’s Cleveland facility are to foreign customers in locations throughout Europe, Canada, Mexico, South America, the Far East and Israel. SIFCO serves this diverse customer base with a responsive and flexible domestic account management team supported by 11 remote sales offices, and in 2022, filled a new international sales manager position to provide direction for these resources and optimal engagement with current and prospective customers. ●
STAHLS’ Transfer Express is a manufacturer of custom heat-applied transfers that are applied with a heat press on apparel and more. The company’s management team has embraced the changing times to move the needle forward in the areas of efficiency, customer satisfaction, employee engagement and overall sales.
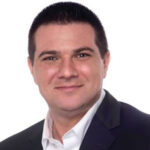
It has evolved the process on its manufacturing floor to be more efficient, while lowering its quality errors and increasing employees’ work-life balance. The company recently moved from its cells being a one-person operation to a team cell. Traditionally, job tasks were performed by a single press operator, many when the press was not running, resulting in a press operating efficiency of only 20 percent. With two operators, the first can focus on quality and registration, while the second performs job prep and cleanup — all while the press is running to increase efficiency to 80 percent.
The changes immediately impacted the business by lowering redo and scrap. Operator 1 now is watching the product most of the time, whereas previously their back was turned doing other work. As more cells were created, it produced transfers more consistently and improved completion time. This continues to drive the work-life balance for all employees and increased volunteers when needed for peak season.
It also reduced utility costs and improved preventive maintenance schedules, and an increase in training and communication assisted with ergonomics as skill levels improved. In addition, the IT department increased the level of automation by utilizing an auto file selection process for screen burning, which increased operator efficiency by 300 percent. ●